Interview with Pete Wagner from Curecrete
- < 3 Ways to Diagnose Your Dying AIA Continuing Education Course
- > Con Job: 3 Ways Product Manufacturers Get Burned from AIA Courses
Today I spoke with Pete Wagner, Director of Supporting Products Development from Curecrete Distribution. We discussed specification strategies for concrete products and what 2018 means for the industry.
What does your company manufacture?
Curecrete manufactures chemicals for the concrete industry. The company started nearly 60 years ago with Ashford Formula, which was the very first chemical densification product for hard steel troweled concrete. We created the first chemical for producing densified and polished concrete in 1999. That product is Retro-Plate.
How does it benefit architects and building projects?
Well, in reality, what we have done is we created a system, so that every product that we make has lineage based off of the original densifiers. We have joint fillers, topical sealants, stain protectants. We have CreteClean Plus which was the first concrete cleaner formulated specifically for densified polished concrete. We also have dyes. I have spent the last 8 months reformulating and recreating our whole dye line. One of my specialties is color.
The reason it benefits the architects as they specify, the owners, and the end users is that it’s environmentally compatible. It provides the opportunity for people to have floors that require no real invasive products to make them perform. The densifiers are water based, so zero VOCs. All the other products are either zero VOCs or fall within the limits. No need for topical coatings or waxes, unless they are using dyes. The dyes attach to the concrete, but you want to use a guard product to allow for cleanup without effecting the integrity of the concrete. Just to provide a window of opportunity to clean up.
Can you please describe what sustainable initiatives your company follows? Sustainable manufacturing? Recycling? Things related to LEED?
All initiatives are within the manufacturing process to minimize or eliminate any by-products or VOCs, that can cause damage. Some VOCs are in the concentrate on the dyes, but they are always within the approved limits. You are not looking at something that you are producing and then you have waste matter from it. Due to us being a liquid, and our large drums being capable of being recycled, we are a minimal waste product. Our two core products, Ashford and RetroPlate have been 3rd party certified that they produce zero VOC’s. Minimizing waste, using recycled materials where compatible and available, and eliminating VOC’s is not only a regulated requirement within our industry, it’s just smart business.
When LEED first came about, we used to be able to contribute in the Innovation category. Which no longer happens, anymore. (laughter) Polished concrete floor provides points under LEED through Proficient Thermal Mass by absorbing thermal warmth through the day and releasing it slowly through the night. No or Low VOCs contribute, as well. It’s a very low maintenance product, and that’s just the beginning.
How do you reach architects?
There’s a little known company out of Washington state...(laughter) There are 4 ways that we reach out. 1 – we do Lunch and Learns ourselves directly, or through our representatives, and we go to Trade Shows. We are involved in having our AIA and GBCI presentations presented through Ron Blank and Associates – CE Academy. And all of these things, and this is not being a wise guy, we do better job of because we always have GreenCE to lean on to make sure we’re always up to speed on the changes in LEED. In fact, one of the areas where we’ve tried to give back is from an educational basis, is that we sponsor the free LEED exam prep on GreenCE.com. The other is that I write articles for several industry publications. Over the last 10 years, I think I’ve written nearly 50 articles in Concrete Surfaces, Green Building & Design, Concrete Décor and Concrete Contractor. One of Curecrete’s goals, from an education standpoint, is to go and help bring everybody up to speed to understand the industry. The industry is young, we are only in our 20th year.
What suggestions do you have for manufacturers and product reps trying to get specified?
Either have somebody in house or have a third party they can count on to make sure they have current knowledge and education so that they are comfortable themselves and can be comfortable sharing, so they don’t misrepresent themselves either naively or intentionally.
When you are looking at doing things, it’s a constant ongoing process, to do things well on a long-term basis. The best thing you can do is to have people acknowledge you for what you do for them that does not outwardly put money in your pocket, you know? Ultimately, if you help someone else be successful in their job, then it’s natural for you to get some benefit out of it. To have someone look at you as a resource, that’s really what you want as a manufacturer, a sales person, or a marketing person. When you are helping them to prosper, to excel in their position, they learn to trust you. But if you misrepresent yourself, or you misrepresent somebody else, well…that’s a long way up to rebuild that trust and that confidence.
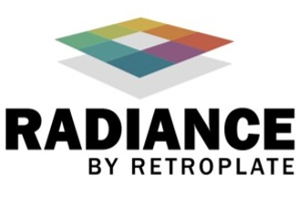
What is your take on the importance of transparency or LEED documentation?
There are benefits to it, but one of the things that makes it tough is that if you as a manufacturer have created a product or a methodology that no one else has made, and the documentation or transparency means you have to disclose to other people how and what you did, I don’t agree with that. You want to provide the information from a safety stand-point, and to meet laws, but you don’t want to go any further.
So, isn’t that where HPDs would come in? You reveal the hazards only, and protect your proprietary information?
I think even HPDs are a little nosy, but I can’t think of anything else out there that works better. It makes up for all of the people claiming ‘proprietary’ on every single thing on their MSD sheet.
What exciting things is your company launching in 2018?
Last year was great with new products, and I printed some articles on that, and they were pretty special. This year, my team and I are really excited about our dye program. We have recreated, appearance, formulation, everything, our dye program. That is something that I had previously been doing as the Marketing Director for RetroPlate and I traveled North America teaching and training about colors and their proper application. In fact, I was known as “The Dye Guy”.
"Radiance" by Retroplate is new. We’ve got 20 colors under the 20 sections, and we also have 5 Shades of Grey. Not 50. (laughter)
I see what you guys did there! How have the dyes worked out?
In the past, what we noticed was that people were taking black and diluting it creating greys with blueish or brownish tints. Through experimentation, knowledge, a little dumb luck. So, we expanded our line to provide our customers what they were desiring. It’s exciting, because no one has had grey before, other than that standard grey. It’s amazing how many floors people just don’t like the standard grey they got.
They way everything works and fits into the system from the cleaner to the dyes, everything builds lineage, which builds strength into the product and how it performs. One of the things that we’ve really tried doing over the last several years is to establish a system where each component you add adds strength and uniformity to the system. So, once it’s down, not only is the end user and the owner excited about it, but it’s performance as far as longevity and minimal maintenance is greatly increased.
You are a great photographer and have shot for many years. Does the love you have for the dyes have to do with you having a photographer’s eye?
I think my love of the dye program does have something to do with my love of the sense of what the light does with color. I got into the flooring industry oh, 35 years ago. I started with a company that had an injection dye system for the color on their carpet tile. I learned a life-long lesson that if you alter the color of concrete with an acid stain that you are literally altering the composition of the concrete. That light source has no effect. If you put dye onto a surface, if changes the reflectivity of the light, as our eye perceives it.
My first custom sample I did was a purple. The designer loved it in their office. When we took it to the job site, it was a different light source, so it looked brown. I won’t use the other terms for what type of brown it looked. (laughter) So, one of the things that I try to make sure that people will understand, is that light source will affect the perception anytime you dye concrete. So, if you are going to do a dye, when it gets approved, it should get approved under the light source of where it is going to be applied.
The other thing is, dyes are translucent - not opaque. That means that whatever color the concrete whether it’s a light grey, or a dark grey, will affect the perception of the color of the dye. So, the lighter the dye is, the more the color of the concrete will deaden it, as our eye perceives it.
I would say my eye for photography, and my sense of composition, also gives me the ability to look at these dyes kind of ‘out of the box’. That is partially how these dyes got created.
Pete can be reached at peter.wagner@curecrete.com or 503.866.1584
For more information or to discuss the topic of this blog, please contact Brad Blank